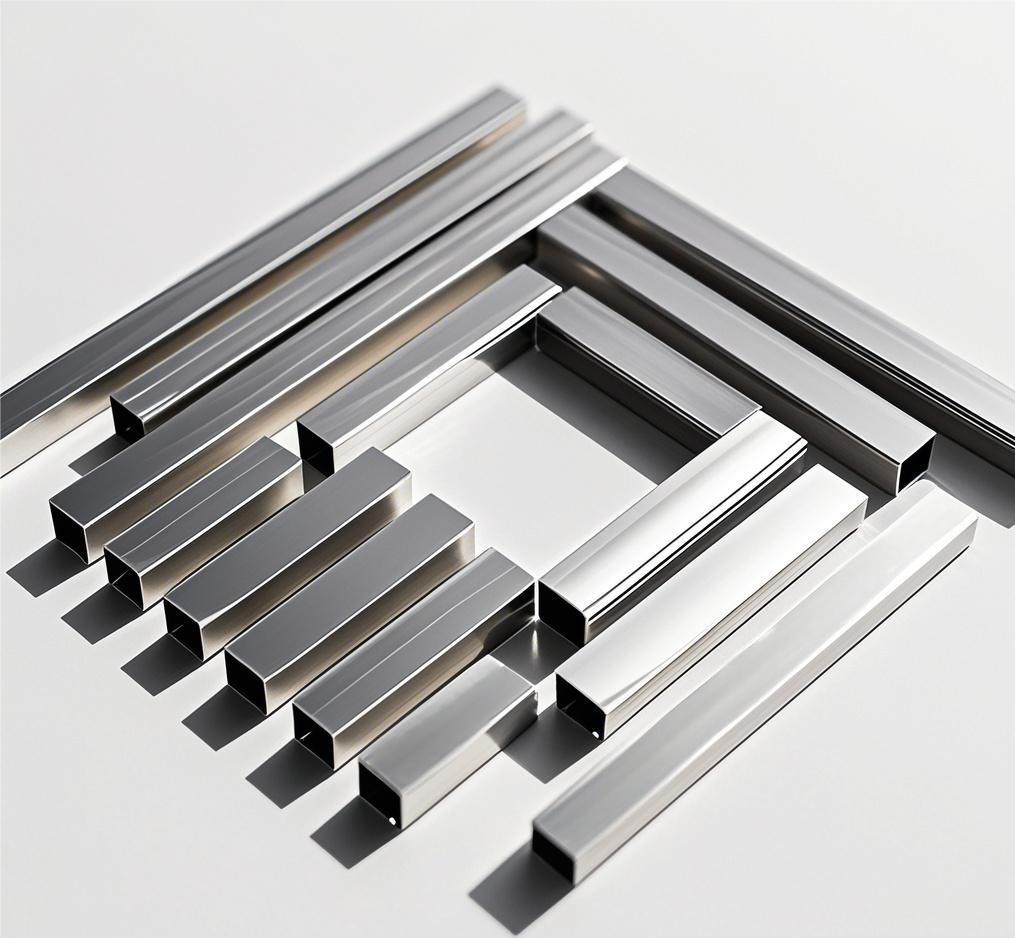
CHEMICAL CONVERSION TECHNOLOGY OF ALUMINUM
Explore aluminum chemical conversion technology, including chromate, phosphating, silane, and eco-friendly chromium-free options.
Aluminum electroplating and chemical plating are two common surface treatment techniques aimed at improving the corrosion resistance, conductivity, wear resistance, ordecorative appearance of aluminum and its alloys. Due to aluminum’s high chemical reactivity(prone to forming surface oxide films) and negative electrode potential, its surfacetreatment processes require special attention to pretreatment steps.
Principles: Deposition of a metallic coating (e.g., nickel, copper, chromium, zinc) onto the aluminumsubstrate through electrolytic reactions.
Challenges: The natural aluminum oxide layer (Al₂O₃) on the surface hinders adhesion of the metal coating. Special pretreatments are required to remove the oxide layer and form a transition layer.
1. Pretreatment:
2. Zinc Immersion Treatment (Critical Step):
3. Pre-Plating Layer: Electroplate an intermediate metal layer (e.g., copper oxide, neutral nickel) to prevent direct contact between aluminum and subsequent coatings, avoiding galvanic corrosion.
4. Target Electroplating: Nickel, chromium, silver, gold, etc. are plated according to requirements (e.g., nickel platingisused for corrosion resistance, chrome plating for wear resistance or decoration).
5. Post-Treatment: Passivation, sealing, or drying.
Advantages:
Disadvantages:
Principles: Deposit a metal layer (e.g.,electroless nickel plating and electroless copper plating)on aluminum by autocatalytic redox reactions without external power.
Applications: Suitable for complex-shaped workpieces, non-conductive substrates, or scenarios requiring uniform coatings.
1. Pretreatment:
2. Electroless nickel plating:
3. Post-Treatment:
Advantages:
Disadvantages:
Comparison | Electroplating | Chemical Plating |
---|---|---|
Plating Metals | Multiple metals (Cu, Ni, Cr, etc.) | Mainly Ni-P, Ni-B, Cu, etc. |
Uniformity | Affected by current distribution | Highly uniform, ideal for complex shapes |
Adhesion | Depends on pretreatment (zinc immersion) | Direct adhesion but requires strict activation |
Environmental Impact | Cyanide/heavy metal wastewater | Phosphorus/heavy metal wastewater |
Cost | High equipment/energy costs | High bath maintenance costs |
Application Scenarios
1. Electroplating:
2. Chemical Plating:
Complete removal of aluminum oxide layers is critical for coatingadhesion.
Both processes involve heavy metal wastewater andrequiretreatment facilities.
Select coating types based on service environment (e.g., electrolessnickel for marine applications).
Explore aluminum chemical conversion technology, including chromate, phosphating, silane, and eco-friendly chromium-free options.
Explore NS2005 superhydrophobic coatings. Stain-resistant, self-cleaning, and durable, ideal for buildings, bridges, and more.